- Overview
- Product Description
- FAQ
- Daily maintenance methods
Basic Info.
Packaging & Delivery
Product Description
Manufacturer Full-Automatic Factory High Temperature Pressure Speed Textile Dyeing Machine for Natural Type Synthetic Blended Fibers |
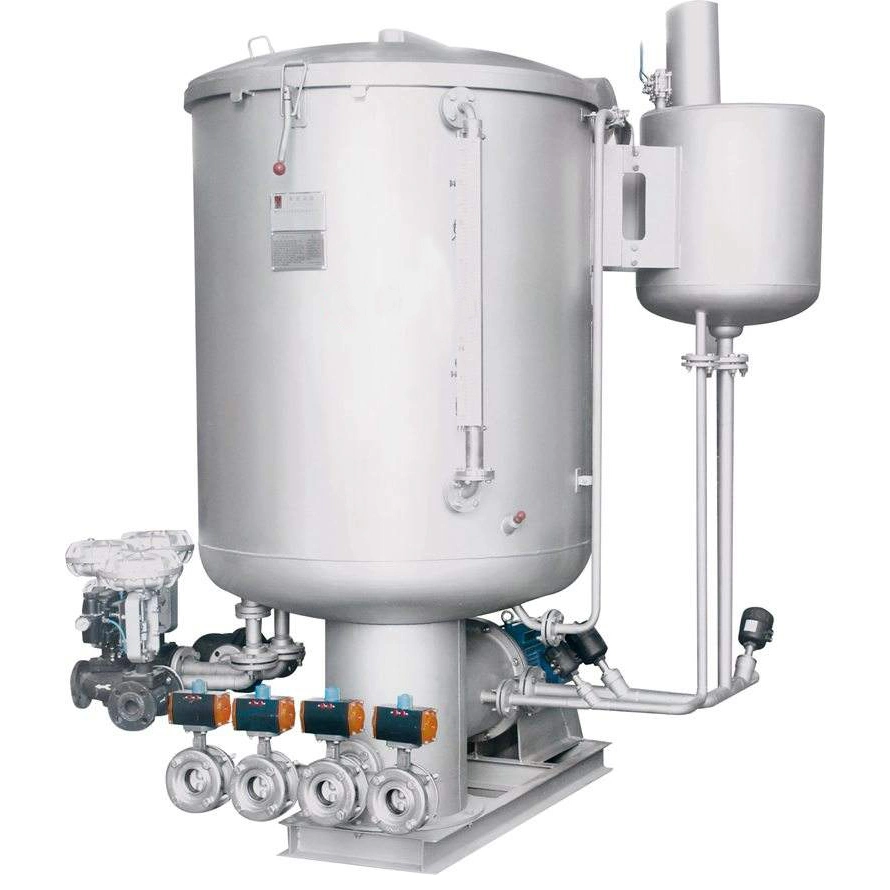
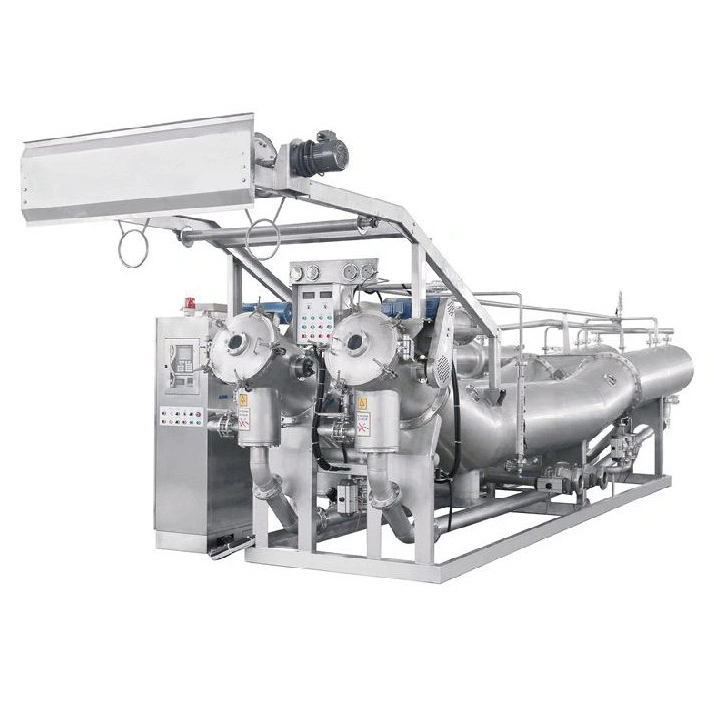
1. The garment dyeing machine is suitable for dyeing and processing of wool, polyester, nylon, artificial fiber, knitted fabric, etc.
2. The liquid cylinder is made of high quality contact and high corrosion resistant 202'' stainless steel plate to ensure no fabric contamination and durability.
3. The inner wall of the dyeing tank and the paddle wheel are surface polished to ensure that the fabric is not damaged.
4. According to the dyeing requirements and heaviness of different fabrics, any high speed rotating paddle can be carried out by the non-for electrical device.
5. The dyeing process is started and stopped by the electric box button. Dyeing time can be controlled and adjusted in advance according to different needs.
6. Automatic control by forward and reverse of power supply to make the paddle wheel in the dyeing tank fall and rotate, so that the liquid flow direction and fabric change to improve the dyeing effect.
7. According to different dyeing process requirements, direct or indirect steam pipeline is installed at the bottom of the tank for heating to achieve the heat preservation effect.
In the past, winch machines were used to dye knitted fabrics, with a material to liquor ratio of 1:20. A soft flow dyeing machine needs only 4 L of water for every 1 kg of fabric processed. Now, a new range of dyeing machines is available with an M:L ratio even lower than 4. In soft flow dyeing machines, the fabrics are circulated using the liquor, which needs some amount of liquor.
Air flow dyeing machines resemble soft flow dyeing machines, with the difference being that the fabrics are circulated using an air stream instead of the water or dye liquor used in the case of soft flow dyeing, thereby reducing the water consumption. The principle of the air flow dyeing machine is based on the aerodynamic principle instead of hydraulics. Air technology is used to transport the fabric during dyeing, washing, and even in unloading. Multinozzle air flow dyeing machines offer higher productivity and drastically reduce the material to liquor ratio to 1:2. The major advantages of soft air flow dyeing machines include:
1.flexible method to transport fabrics using air;
2.able to process fabric weights ranging between 50 and 800 g per square meter;
3.extremely low material to liquor ratio of 1:2 for MMF and 1:3-1:4 for natural fibers;
4.nearly 40% of energy saved when compared with soft flow dyeing machines;
5.reduced process time up to 25%.
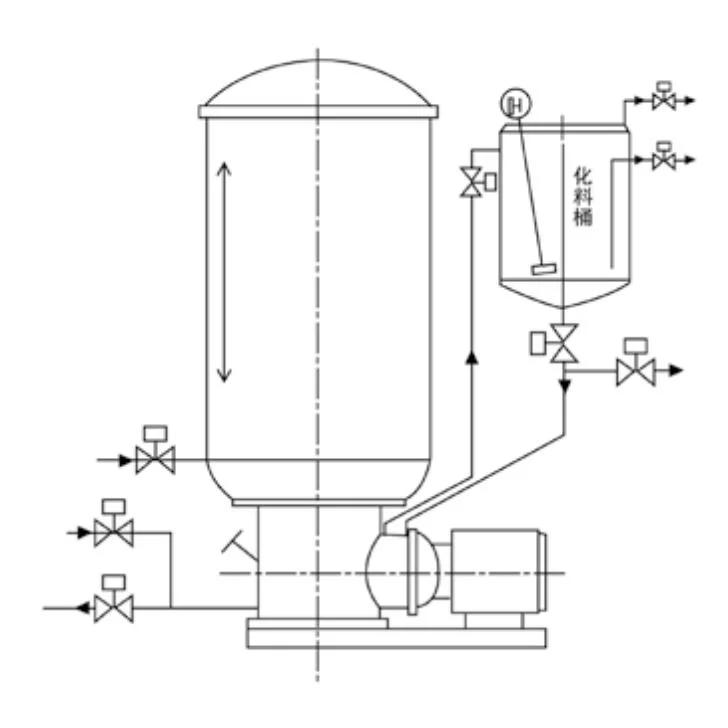
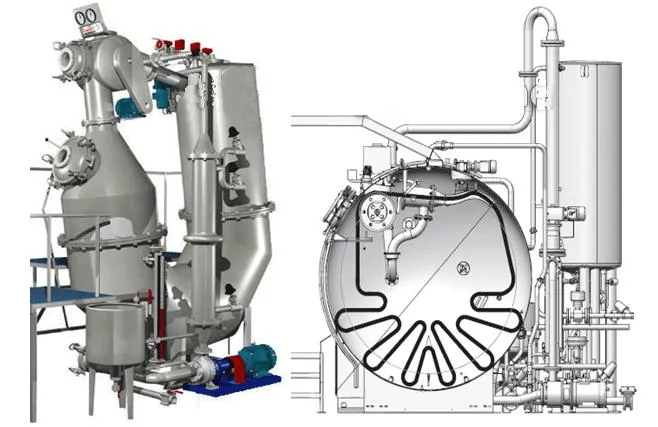
Q1.Can you provide OEM service?
we can provide OEM service. It will depend on your requests,your logo will be customized on our products.
Q2.How many days about delivery time?
15-20 days after TT deposit.
Q3.What is the packing?
General machines are with vacuum packing. Particular machine are packing with vacuum and wooden case. Container loads as per the machine size.
Q4. What information may contain in my inquiry?
Your request your machine's embroidery area /needle number /head number/head interval/other function need.
Q5. Do you test all your goods before delivery?
Yes, we have 100% test before delivery
Q6.How to insatll and use the embroidery machine?
We have the English teaching manual and videos;The videos about every step of machine Disassembly, assembly, operation.
Q7: How do you make our business long-term and good relationship?
1. We keep good quality and competitive price to ensure our customers benefit ;
2. We respect every customer as our friend and we sincerely do business and make friends with them.
(1) use a brush to clean the rotating shuttle, shuttle shell and shuttle core of the hooking mechanism. Do not use sharp and hard tools to remove sundries and threads.
(2) remove sundries and thread ends at the height of wire rod, wire channel and felt;
(3) four pairs of guide rail (type 615) in front and rear of Y-axis feeding mechanism are on the same plane;
(4) two X-axis feeding mechanism guide rails are on the same plane;
(5) wire clip mechanism, wire clip, rotating wheel, wire pick, spring and wire channel are often cleaned up;
(6) cleaning sundries on the surface of work surface;
(7) the surface of the computer and the exhaust fan are often rubbed and the back cover is opened;
(8) power box, drive box surface and ventilation are often as above.